From the Drawing Board to 200 Meters Undersea

Company: Paralenz
Industry: Engineering
Profile: Michael Trøst and the team behind the Paralenz dive camera set out to create a durable, easy-to-use underwater action camera that delivers high-quality footage, even from extreme depths.
Challenge: Developing a compact diving camera required dozens of iterations and accurate, high-quality prototypes. The team had to design for manufacturability, so it was crucial that their prototyping tool could emulate the final manufacturing process.
Solution: Using the Form 2, Paralenz managed to create prototypes that look, feel, and work like the final product throughout the entire development process, from designing to testing and manufacturing.
Results:
- 20-25 high-quality housing iterations produced in-house in just a few months.
- Over $10,000 saved in outsourcing costs.
- 3D printed prototypes and parts simplified communication with the 17 suppliers that manufacture custom parts for the product.
Company: Paralenz
Industry: Engineering
Profile: Michael Trøst and the team behind the Paralenz dive camera set out to create a durable, easy-to-use underwater action camera that delivers high-quality footage, even from extreme depths.
Challenge: Developing a compact diving camera required dozens of iterations and accurate, high-quality prototypes. The team had to design for manufacturability, so it was crucial that their prototyping tool could emulate the final manufacturing process.
Solution: Using the Form 2, Paralenz managed to create prototypes that look, feel, and work like the final product throughout the entire development process, from designing to testing and manufacturing.
Results:
- 20-25 high-quality housing iterations produced in-house in just a few months.
- Over $10,000 saved in outsourcing costs.
- 3D printed prototypes and parts simplified communication with the 17 suppliers that manufacture custom parts for the product.
A peek into the design and development process at Paralenz, featuring fully 3D printed prototypes of the dive camera and its accessories created using a Form 2.
Profile
Michael Trøst and the team behind the Paralenz dive camera have been involved in product development and consultancy for more than 15 years. When their colleague Martin, an avid diver, saw a gap in the market between all-round action cameras and high-end diving cameras, they decided it was an opportunity.
Months of research, development, and design iterations followed. The team set out to create a durable, easy-to-use underwater action camera that delivers high-quality footage, even from extreme depths.
Using the Form 2 stereolithography (SLA) 3D printer, Paralenz managed to create astonishing prototypes that look, feel, and work like the final product. The team relied on 3D printing throughout the entire development process from designing to testing and manufacturing.
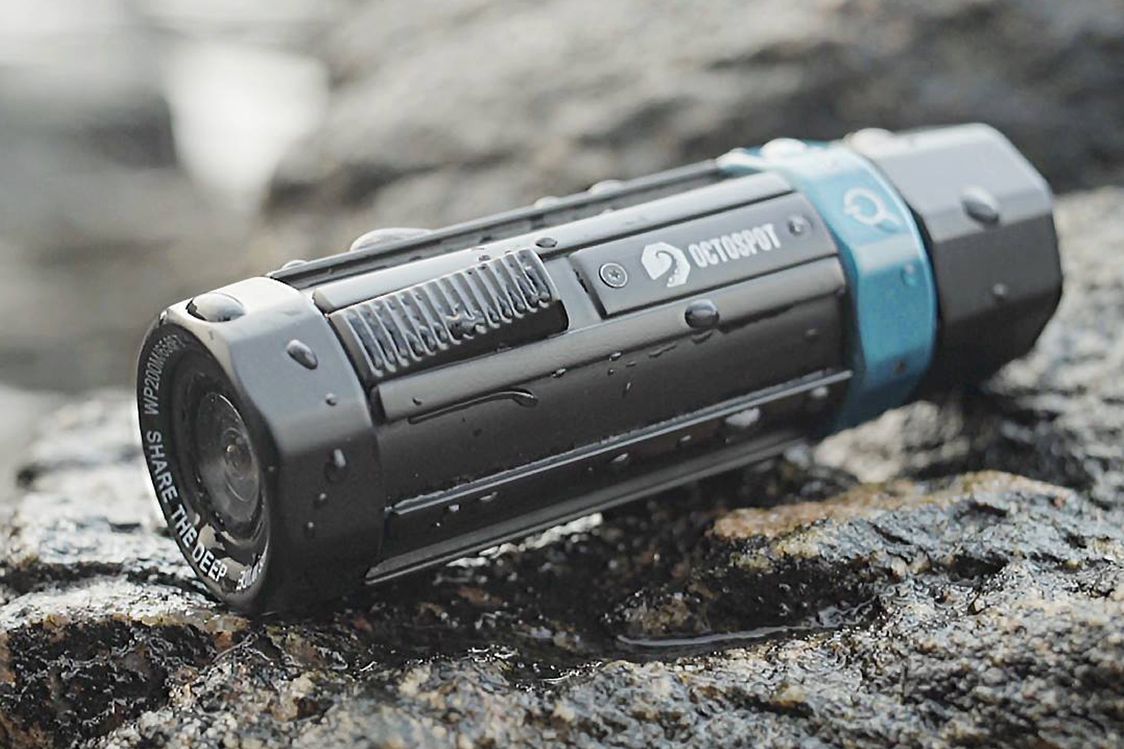
Paralenz’s prototypes look, feel, and work like the final product.
Challenge
Paralenz had previously used outsourced SLA and in-house fused deposition modeling (FDM) 3D printing for prototyping. Outsourcing to service providers was slow and costly, while FDM proved unreliable and not accurate enough for the compact parts of the camera.
“Before we had the Form 2, we’d start three machines just to make sure that one of them worked. You would come in the day after you needed the part, but it was not finished because the machine failed in some way. The Form 2 is the first 3D printer we dare rely on. So far we have had maybe one failed job out of more than 200.”
The team had to design for manufacturability, so it was crucial that their prototyping tool could emulate the final manufacturing process, without having to modify the parts for 3D printing.
“With the Form 2, if you make something that’s round in CAD, it’ll come out round when printed. If we split into different pockets, it fits, and even the threads fit. Having tested all parts for form and fit gave us confidence moving into manufacturing.”

Parts printed with White and Black Formlabs Standard Resin, straight out of the Form 2 and post-processed.
Solution
Paralenz used the Form 2 to print different size models to evaluate the volume, weight, and ergonomics—altogether cycling through seven or eight designs. All the parts of the prototypes are 3D printed, except the lenses, which are cast in a silicone mold using a 3D printed master. They tested the prototypes with divers, and iterated and gathered feedback on different versions of individual pieces of the camera, such as the the button.
“The Form 2 saves us man hours, because it's closer to being finished straight out of the machine. FDM models take about three times as long to get a high-end finish, and with a lot of parts you cannot even get the same finish on those models, regardless of the amount of work. Before we’d also have to do lot of tasks by hand or by CNC milling, which require additional skills.”
Paralenz even used the prototypes for tests in a pressure tank and real-life tests diving in the sea. The 3D prints were tested to 150 m in salt water without any problems.

Once printed, the enclosure is cleaned, sanded, and painted. To cast the lens, Trøst used a 3D printed master for the mold. The logos are printed on an inkjet printer.
Results
As the diving camera is quite a compact product, the team spent a lot of time figuring out how to optimize the design, while making sure that it accommodated all the required features. Having the Form 2 in-house enabled them to iterate about 20-25 housings in a matter of a few months.
“Working with the Form 2 has also saved us quite a lot of money. We used to have a large budget for SLA models; for this project alone, we’d have spent $15,000 on SLA parts. Buying a Form 2 and all the materials was less than third of that, so it has already paid backthe initial investment multiple times.”
The prototypes also helped the team to simplify communication, coordinate, and reduce risks when working with manufacturers abroad. Paralenz used 17 different suppliers that all make custom parts; so it was vital to ensure that everyone was on the same page.
The team used the final 3D printed prototypes and parts to make it easier to communicate the product and its intricacies to each manufacturer. It was especially beneficial to tangibly demonstrate parts that had to fit together, instead of just showing 3D models.
“Communication and coordination errors with manufacturers in other countries, especially when talking about in-depth technical details, can be very costly; even the smallest miscommunicationcan set back development by a week—critical missteps by much longer. Having the actual parts made it much easier for people understand the product in the first place.”
Application Outsourcing 3D printing on the Form 2 Paralenz Camera Prototype 1–2 weeks 10X 1X 1–2 weeks 1–2 weeks 1 day

Paralenz’s high fidelity prototypes and parts, ready for showcasing.

The detachable third-person viewer for the camera, which floats behind the diver, was also prototyped on the Form 2.
Using high fidelity prototypes 3D printed on a Form 2, Paralenz saved over $10,000 in outsourcing costs and months of lead time over the course of the development of their dive camera, and also simplified communication with manufacturers.